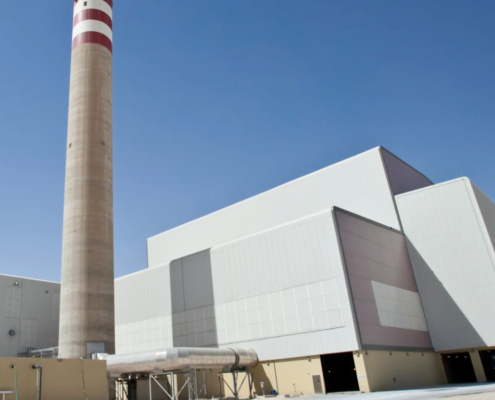
A pioneering leap: Qatar’s integrated domestic solid waste management centre
Location: Qatar
Category: Integrated Waste Management Facility
Contract type: Design, Build and Operate – DBO (20 years, start operation in 2011)
Scope of contract: Waste sorting and recycling, Composting, Anaerobic digestion, Waste to Energy and Electricity production.
Number of Production Lines: 3 water cooled production lines handling each 500 tonnes per day
Capacity: 2300 tons par day incoming waste from which 800 are recycled or composted, and 1500 are converted in energy.
In the heart of the Middle East, Qatar has embarked on an ambitious journey to tackle one of the most pressing challenges of our times: waste management. The Qatar Integrated Domestic Solid Waste Management Centre stands as proof to this commitment, pioneering a holistic approach to managing the country’s solid waste. This facility is not merely a project but a bold statement by the Qatar Government, signifying a move towards sustainable and integrated waste management solutions.
DBO contract for 20 years
Conceived and executed by Keppel Seghers, the project commenced operations in 2011, following a construction period that spanned from 2007. Entrusted with a design, build, and operate (DBO) contract for 20 years, the project marked a significant step towards innovation in waste management. It was designed to address the dual challenge of reducing the volume of waste ending up in landfills while optimising resource recovery from waste.
A facility unlike any other
Strategically located in Qatar, the WtE plant integrates several state-of-the-art processes including waste sorting and recycling, composting, anaerobic digestion, and Waste-to-Energy conversion, making it the first of its kind in the Middle East. The facility operates with an impressive capacity, handling 2,300 tonnes of incoming waste daily. Of this, 800 tonnes are either recycled or composted, while the remaining 1,500 tonnes are converted into energy.
95%
Waste recycling or recovery
20 years
Operation and maintenance
1st
In Middle East
Let’s talk numbers
At its core, the facility boasts three production lines, each with a capacity of 500 tonnes per day, equipped with water cooling systems. The technology employed is at the cutting edge. A horizontal rotating steel cylinder with integrated screens segregates municipal solid waste into three fractions: organic waste for anaerobic digestion and composting; medium-sized waste for sorting and recycling; and larger waste for energy conversion.
Recycling and recovery
In the recycling segment, the plant excels in efficiency, separating ferrous and non-ferrous metals, and various types of plastics for recycling. The anaerobic digestion and composting plant not only handles 750 tonnes of waste daily but also generates up to 109,000m³ of biogas, translating into 6.8MW of green electricity and heating.
Energy generation
The Waste-to-Energy plant is capable of processing 1,500 tonnes of waste per day. It features three water-cooled combustion grates, a horizontal boiler powering a 42MW steam turbine, and a comprehensive flue gas treatment system with continuous emission monitoring.
Harnessing technological synergies
The strength of an integrated waste management concept is the combination of several technologies in one installation. The combination of pre-processing, mechanical and organic recycling and power-generating technologies offers synergy which would be unattainable if each technology was employed individually.
This synergy leads to more energy and material recovery, and a maximum landfill diversion of up to 95 percent.
An integrated waste management system
A crucial aspect of an integrated waste management system is the initial pre-processing of the incoming waste. This step involves sorting materials appropriate for various treatments like recycling and energy recovery via Waste-to-Energy (WTE) technology. By directing materials to their designated processing streams, pre-processing ensures optimal performance and maximises the value extracted from each segment of waste.
Challenges overcome
The journey to the realisation of this facility was not without its challenges. Constructed under the harsh desert conditions of Qatar, with temperatures soaring above 45°C, high humidity, and frequent sandstorms, the project demanded solutions that could withstand extreme conditions. Keppel Seghers’ technology proved up to the task, ensuring the plant’s operational resilience and efficiency.
Forward-thinking initiatives
Current research and development projects at the Qatar Integrated Domestic Solid Waste Management Centre focus on the treatment of solid residues from the Waste-to-Energy process. These initiatives include further recovery of metals, brick manufacturing, and their use in pavement and road applications, showcasing a commitment to continuous improvement and sustainability in waste management practices.
Highlights
-
95% of the incoming waste is either recycled, composted or converted into energy, showcasing the centre’s efficiency in waste processing and resource recovery.
-
The facility sprawls across a 300ha site, underlining the scale and ambition of Qatar’s waste management strategy.
-
The highest record of 50.4 °C (122.7 °F) in July 2010, coupled with high humidity, underscores the extreme environmental conditions under which the facility operates, demonstrating its resilience and the robustness of the technology employed.