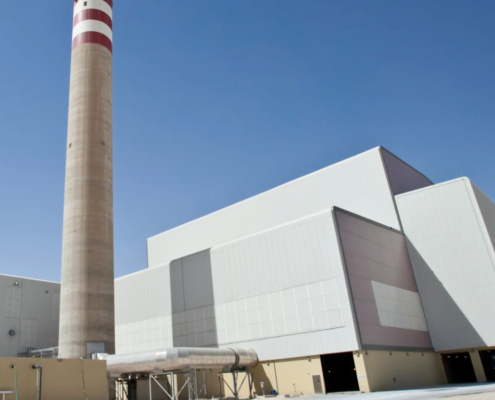
Eco-majesty: Unveiling the world’s largest Waste-to-Energy powerhouse
Location: Shenzen, Guangdong
Category: Waste-to-Energy and Recycling Plants
Contract type: Technology supply
Scope of contract: Technology provider
Number of Production Lines: 12 SIGMATRIX waste combustion lines
Construction period including several phases: 2006, 2013, 2018
Unprecedented scale and historical impact
The Bao An Waste-to-Energy plant emerged as a monumental figure within the industry, unparalleled in size and capacity. It annually processed a staggering 3 million tonnes of waste—nearly 9,000 tonnes per day. Had it been likened to a mythical creature, it would have undoubtedly been considered a dragon, both for its immense capacity and its monumental impact on waste management and energy production. The Phase III expansion, completed by 2018, elevated its daily processing capability to 8,875 tonnes, establishing it as an unrivaled facility worldwide.
Decades of partnership and innovation
Over two decades, Keppel Seghers played a crucial role in the expansion of China’s Waste-to-Energy sector, contributing through the strategic importation of crucial technology—specifically, the combustion grate and its accessories. This approach fostered strong partnerships with local partners, notably with Shenzhen Energy Environmental Engineering (SEEE). SEEE had entrusted Keppel Seghers with the development of all three phases of the Bao An plant, a testament to the latter’s superior technology and performance. From the pioneering first phase to the revolutionary 1,000 ton per day capacity line in Phase III, Keppel Seghers led this evolutionary journey.
12
production lines
200MW
Electricity production capacity
3Mio
households per year
A legacy of technological excellence and recognition
The Bao An facility was not just the world’s largest by capacity, at 8,880 tons per day, but also a beacon of technological excellence and environmental stewardship. Phase I marked Keppel Seghers’s entry into China’s Waste-to-Energy scene, setting a high benchmark from the start. Phase II not only upheld but elevated this standard, earning the prestigious Gold Medal for the National Outstanding Engineering Award in 2014. This phase became widely regarded as a benchmark for Waste-to-Energy facilities in China, celebrated for its reliability and innovative technology.
Revolutionary technology for optimal flexibility
Keppel Seghers’s technology was celebrated for its flexibility, a crucial attribute for handling the diverse waste profiles encountered in large-scale operations. The Bao An Phase III exemplified this, featuring six lanes of modular combustion grates. This modularity allowed for precise control over the combustion process, accommodating variances in waste moisture and composition. Such innovation not only enhanced the plant’s efficiency but also established a new standard in Waste-to-Energy processing.
Mastering the complexities of international collaboration
Engaging with China’s burgeoning Waste-to-Energy market required a nuanced approach, balancing the import of core technologies with leveraging local production and expertise. Keppel Seghers adeptly navigated this landscape, focusing on delivering essential components like the grate, hydraulics, and burners, while local partners managed the remaining construction scope. This collaborative model facilitated Keppel Seghers’s success in China and underscored the importance of innovation and rapid adaptation in a competitive environment.
Reflecting on a sustainable future
As Keppel Seghers continued to expand its footprint in China, the success of the Bao An plant stood as a shining example of what could be achieved through international collaboration, technological innovation, and a deep commitment to sustainability. With the world’s largest Waste-to-Energy plant as a milestone, Keppel Seghers was poised to lead the charge towards a cleaner, more sustainable future in waste management and energy production.
Highlights
-
The plant processes 3 million tons of waste each year.
-
It generates 200 MW of electricity, enough to supply power to 1 million citizens.
-
Phase 3 includes five SIGMATRIX waste combustion lines, each capable of treating 1,000 tons of waste per day.